More manufacturers experienced a failure in testing for the 2023 Scorecard than in the previous edition; however, both were lower than what was reported in the 2021 Scorecard. The BOM-level failure rate increased with 32% of BOMs experiencing at least one failure, up from 26% in the 2021 and 2022 Scorecards. The largest increase was for initial (pre-stress) and thermal cycling failure rates, which both more than doubled from the 2022 Scorecard.
Failures in Testing
Why Module Failures Matter
Site acceptance testing was performed by Extel Energy, a member of the Kiwa Group, on a 12 MW rooftop site in Taiwan. The project used 340W half-cut 120-cell mono PERC modules and was commissioned in 2021. Routine drone infrared (IR) imaging revealed hot spots at the junction boxes for some modules, along with some activated bypass diodes. Upon further inspection of the site, Extel found some completely burnt junction boxes. Of the ~35,000 modules on site, ~700 had hot spots at the junction boxes visible in IR images, ~70 had bypass diodes activated and ~10 had extreme junction box burning.
The module manufacturer investigated and determined that these were all due to a soldering issue within the junction box. They updated their quality and process control to implement pull testing on their junction box soldering.
While replacements for the affected modules were provided by the manufacturer, the cost of labor to replace these modules and to diagnose the issue was not covered by the module manufacturer’s warranty. It is unclear if other modules will be affected by this failure mode in the future, given that they will experience natural temperature cycling in the field and its effects on soldering reliability.
PVEL has reported junction box related failure issues in every edition of the Scorecard since 2019. This problem still remains persistent both in the failures identified by PQP testing and on modules in the field.
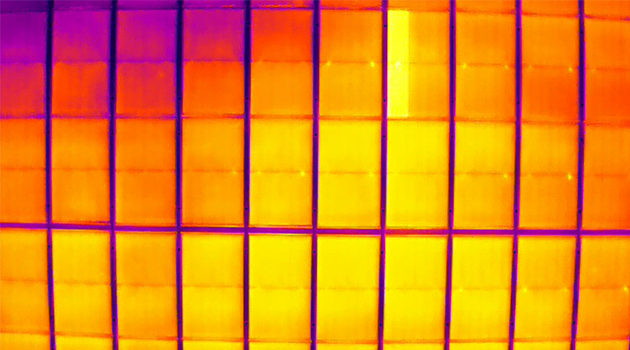
Infrared image showing junction box hot spots (via the brighter dots on the modules), and one module with an activated bypass diode (via the bright rectangle on module located in the top row, fourth from the right).
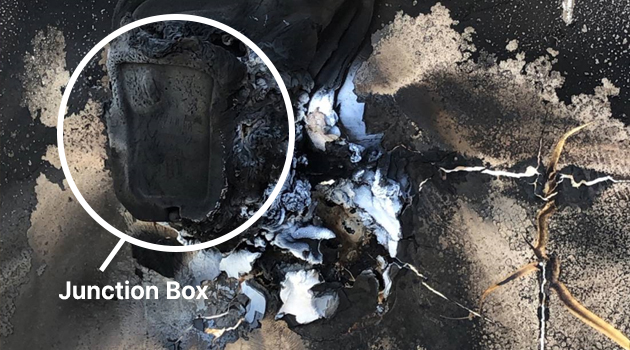
An example of one of the ~10 modules with extreme junction box failure due to electrical arcing.
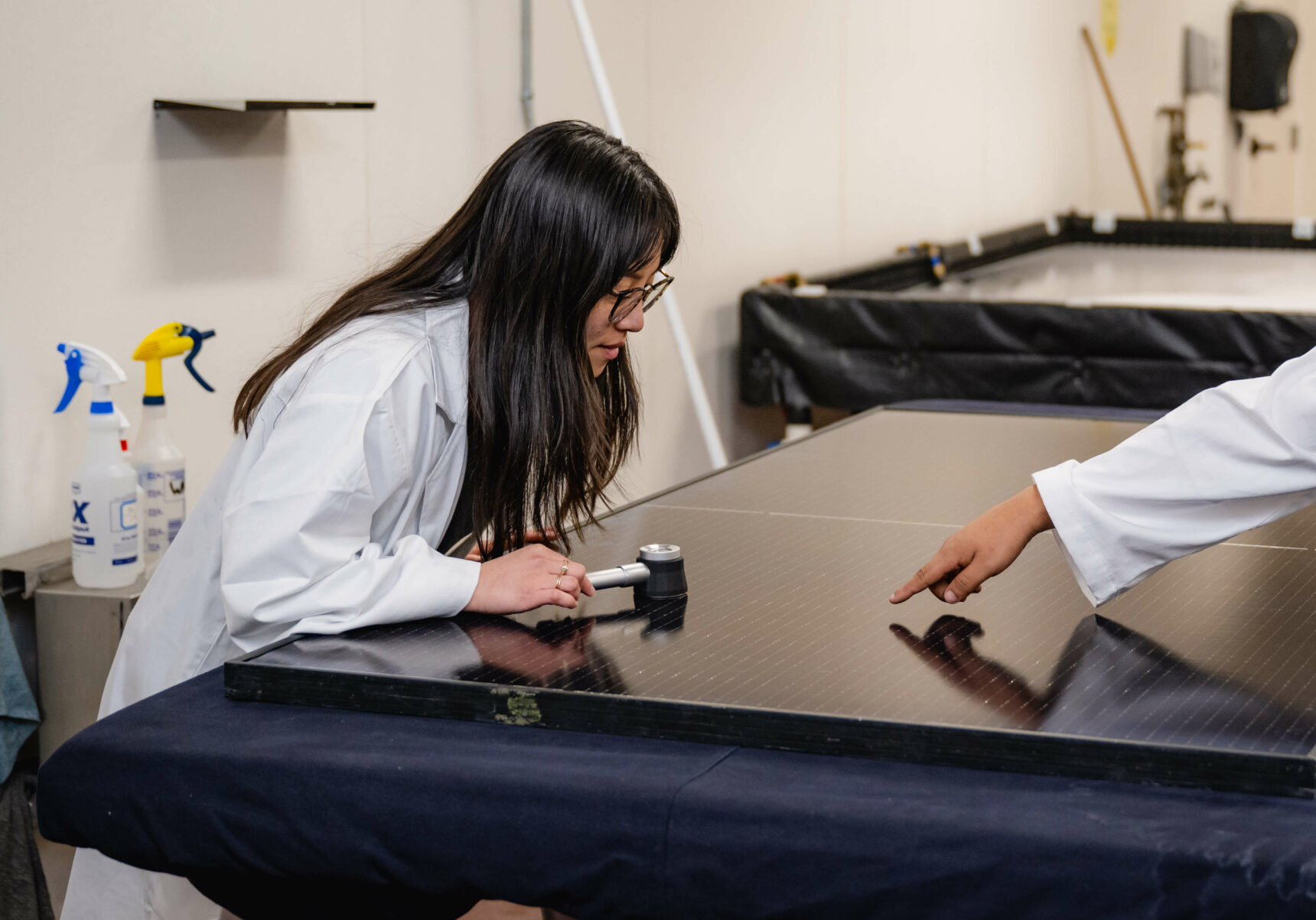
40% of manufacturers and 22% of BOMs had a failure found during visual inspection.
23% of manufacturers and 18% of BOMs had a safety failure.
17% of manufacturers and 9% of BOMs had a power degradation failure.
29% of manufacturers and 19% of BOMs had a junction box related failure.
PQP Failure Statistics
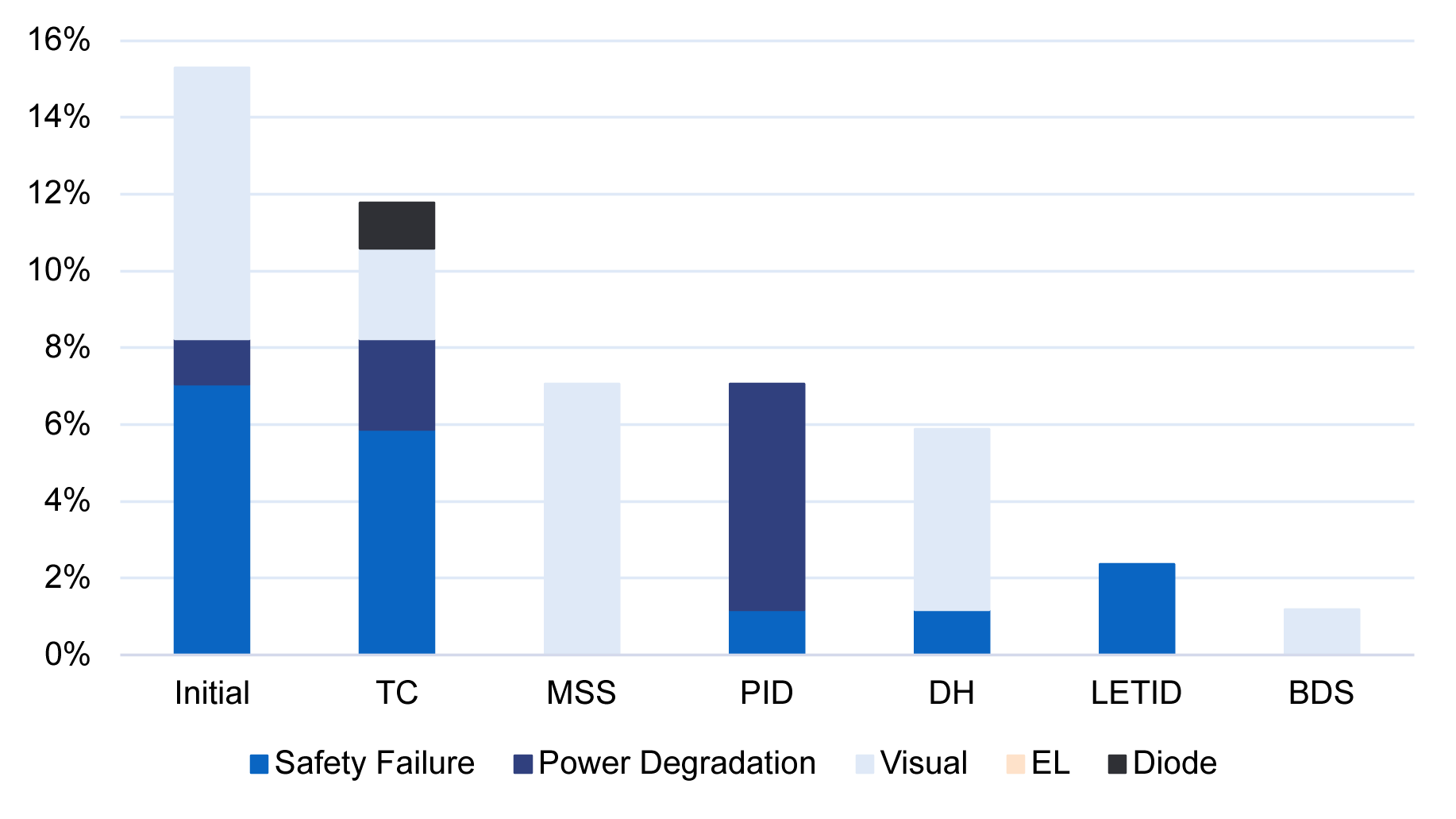
This graph shows the percentage of BOMs experiencing a failure in each test sequence of the PQP by failure type.
The most common type of failure is visual inspection major defect, followed closely by safety failures due to low insulation resistance.
Initial failures are those that were detected during characterizations prior to stress-testing.
HSS failures are not shown. Visit the HSS page to learn more.