PVEL’s approach to testing and benchmarking PV module reliability has been our key focus for more than a decade. The PQP results enable data-driven solar procurement and investments for developers, financiers, and asset owners.
Methodology
Go Inside a PV Module
Although Top Performers are listed in the Scorecard by model type, they represent unique bills of materials (BOMs) that PVEL has tested in our Product Qualification Program (PQP).
Scroll to explore the materials of a PV module. Click on labels to see how many types of each component were used in the BOMs tested for the 2023 Scorecard.
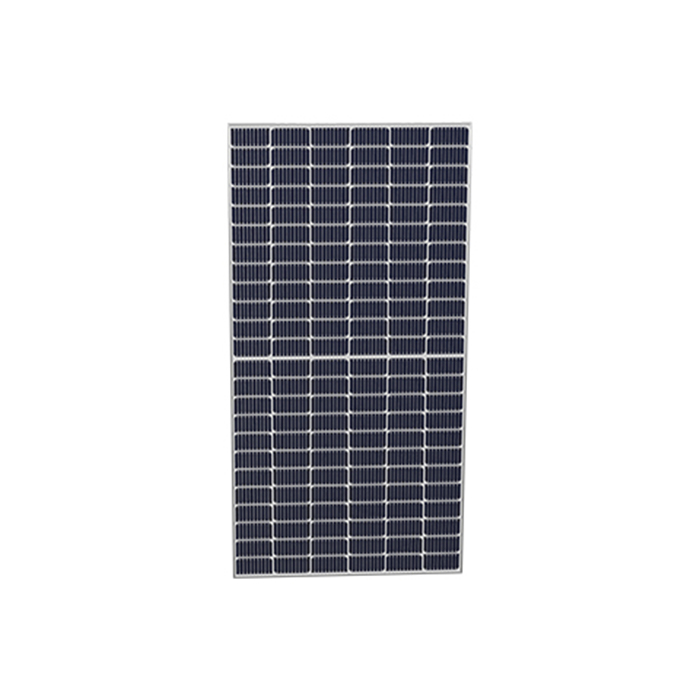
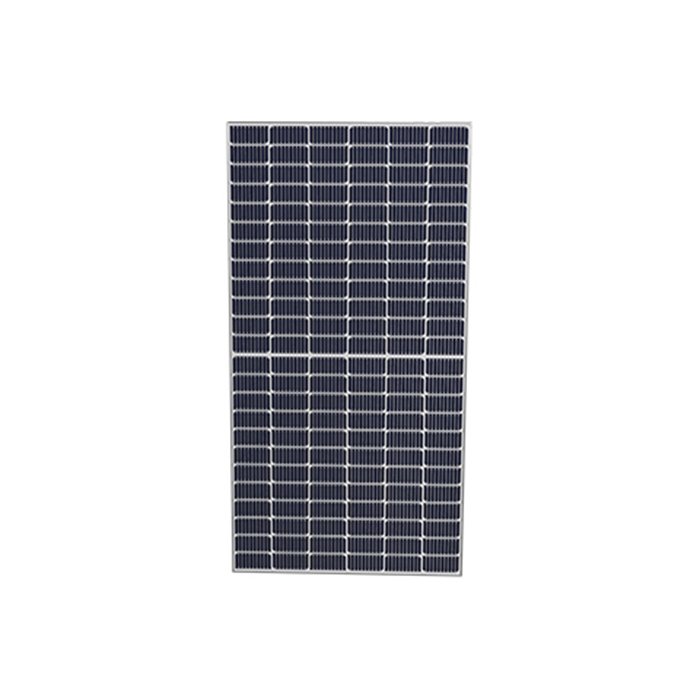
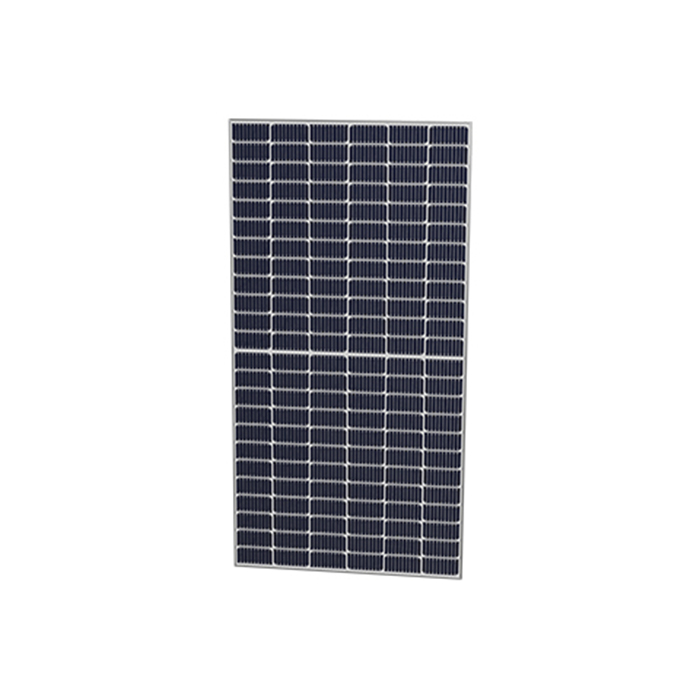

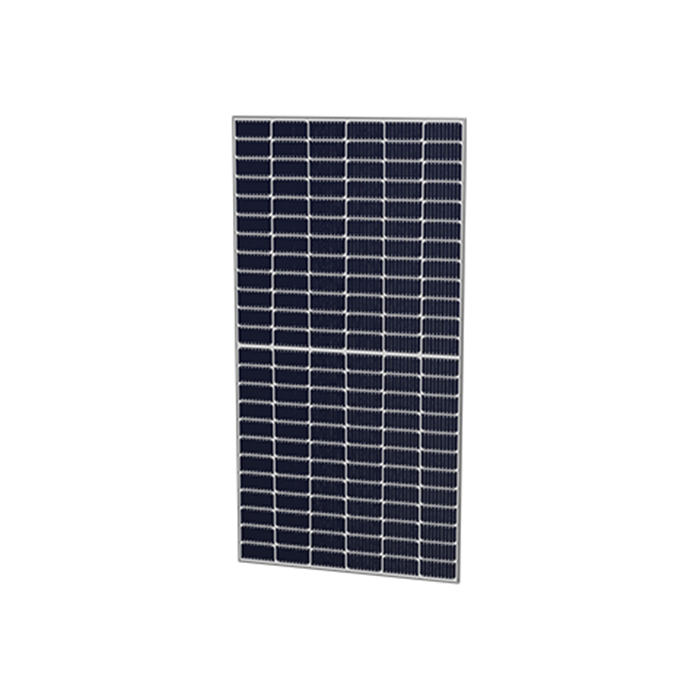
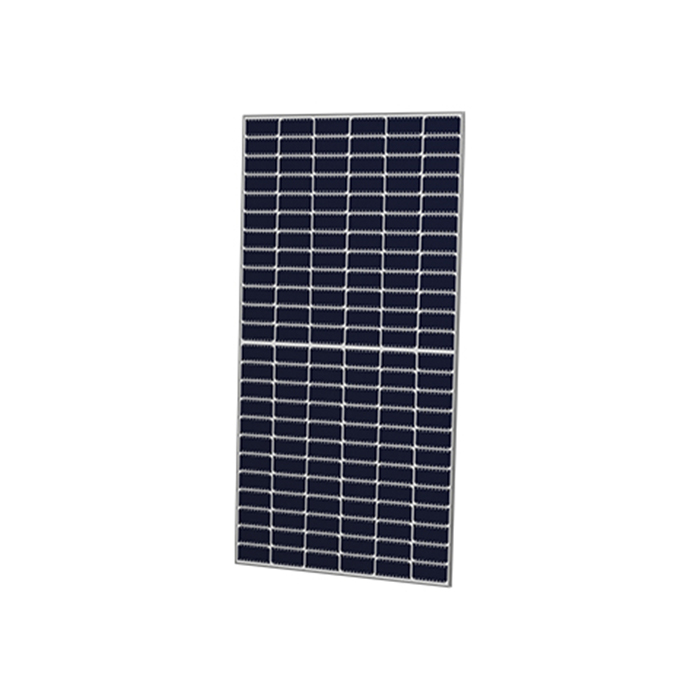
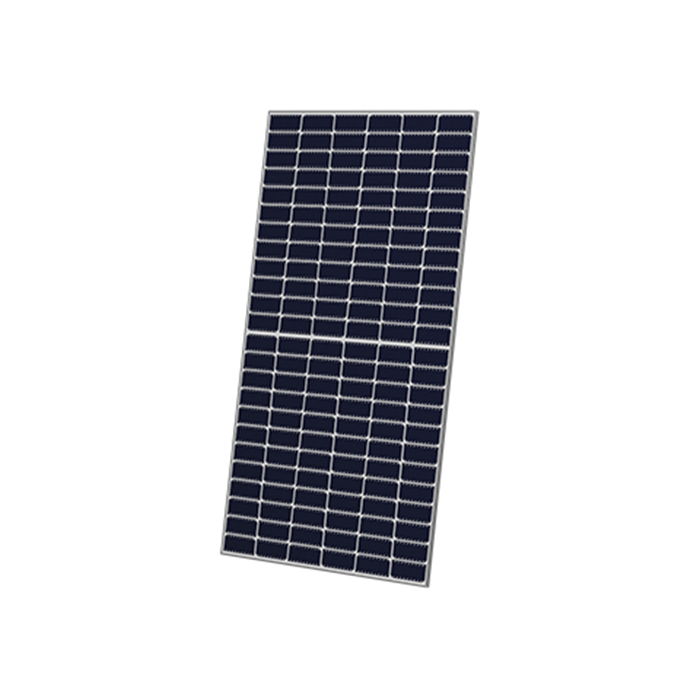
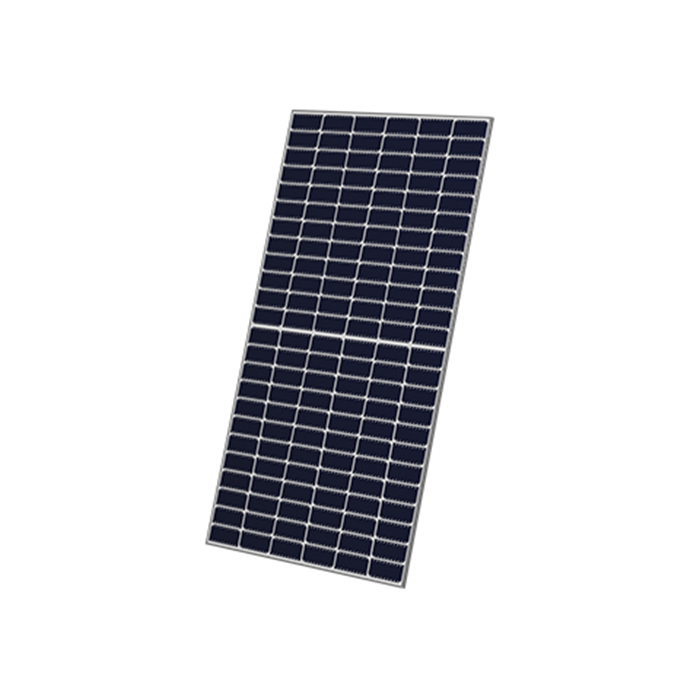
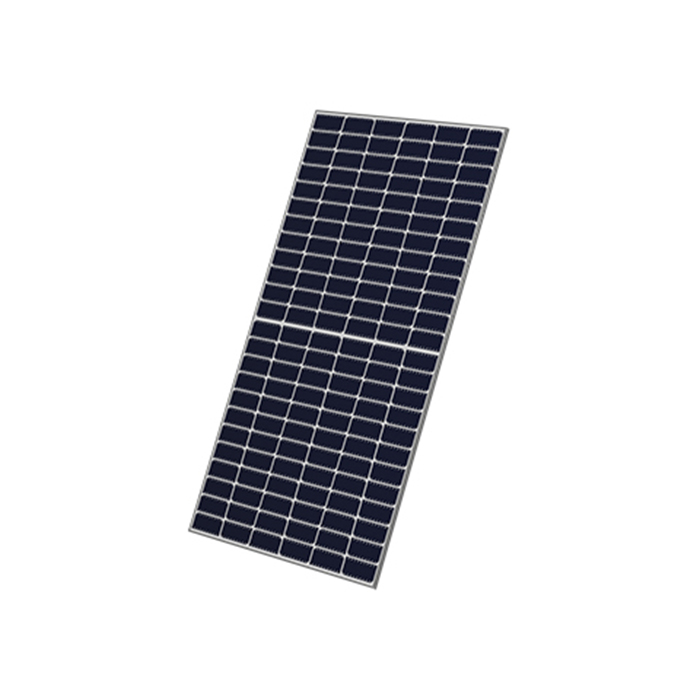
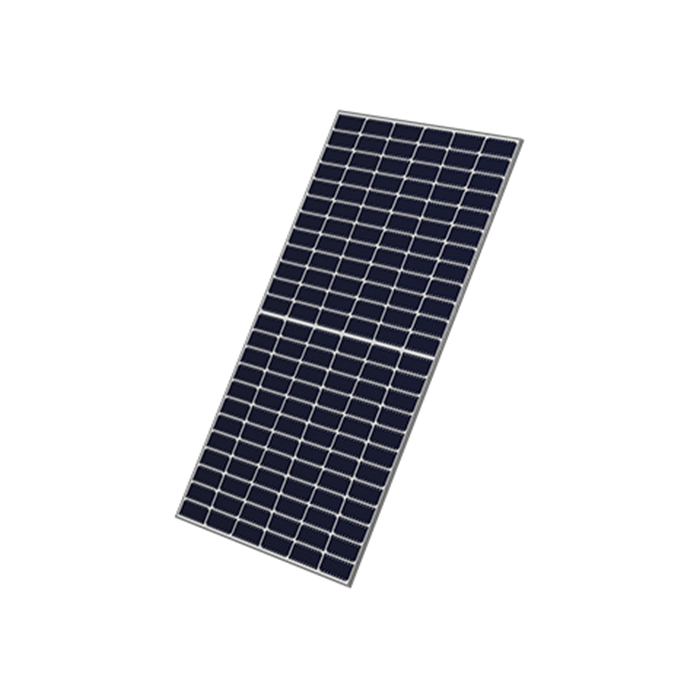
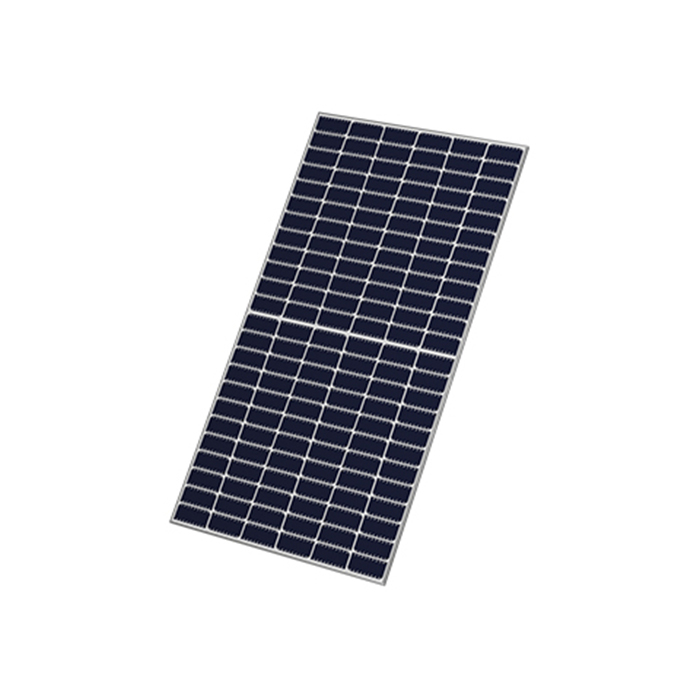
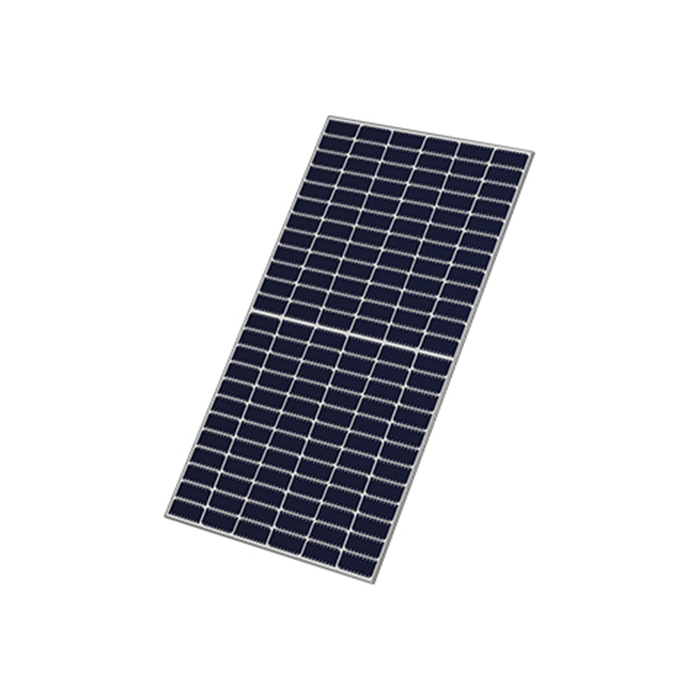
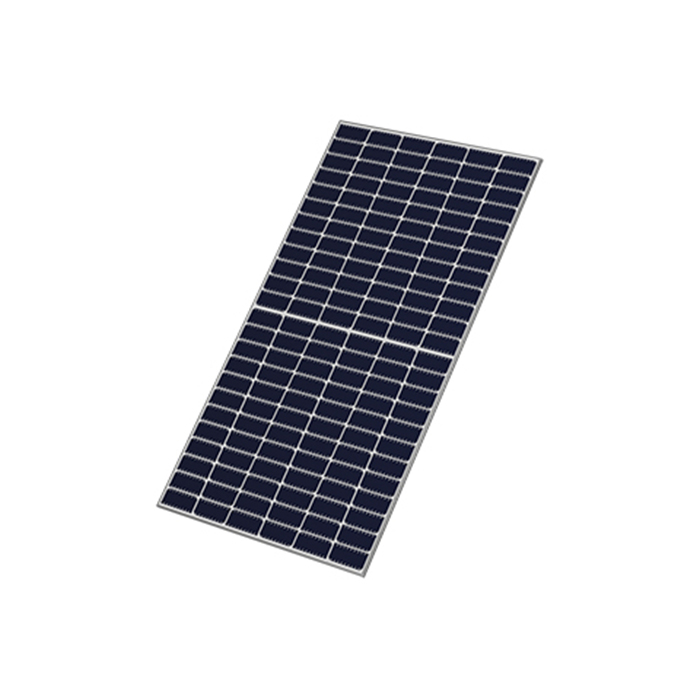
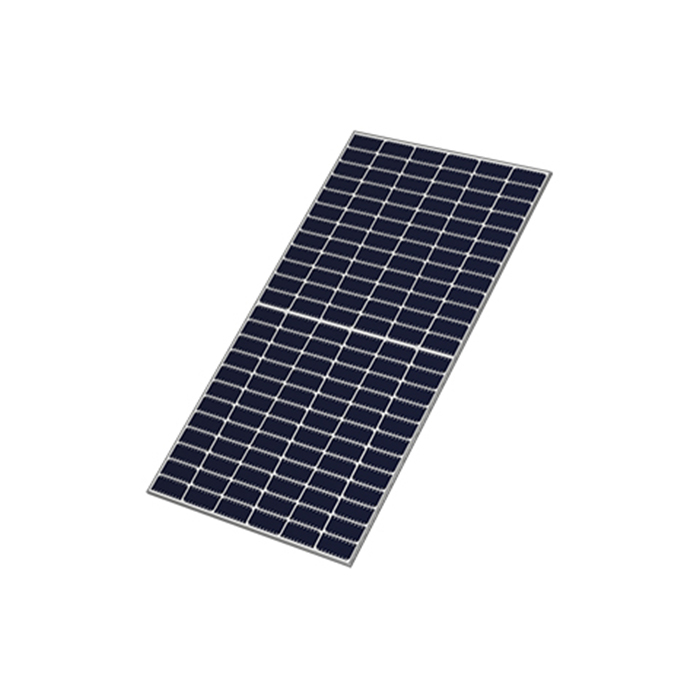
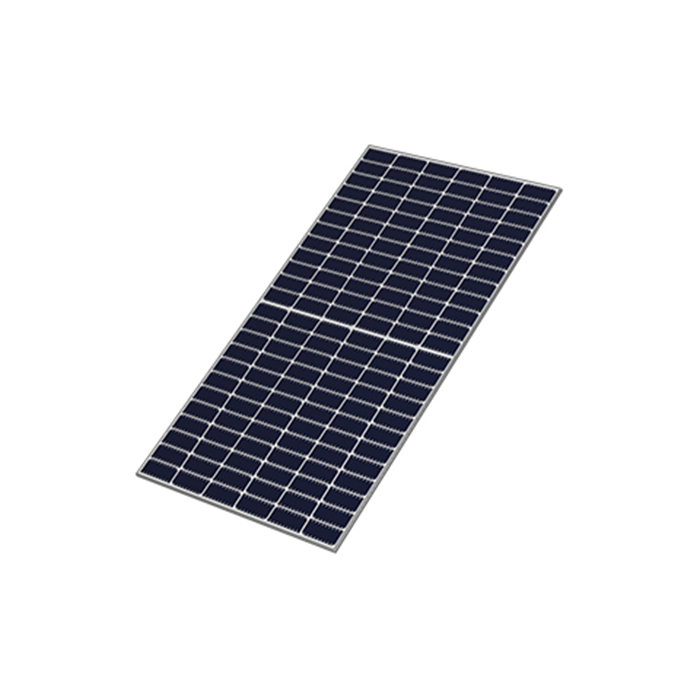
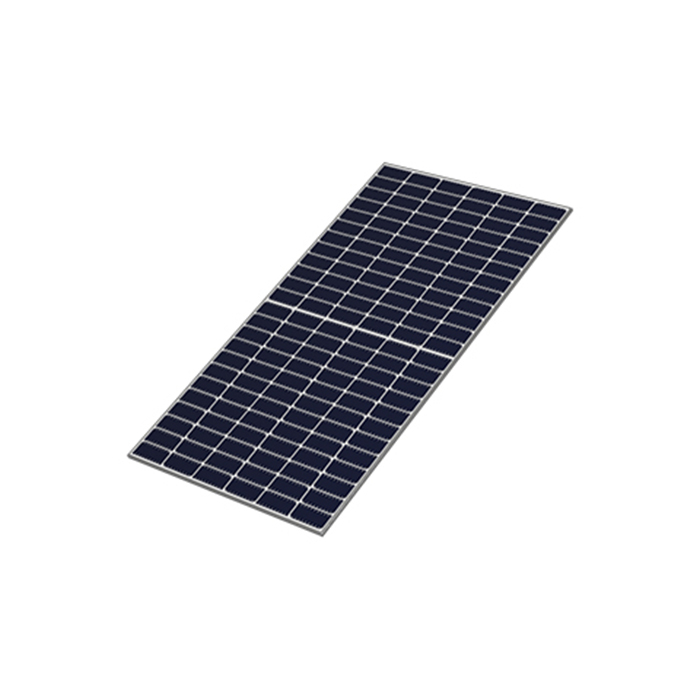
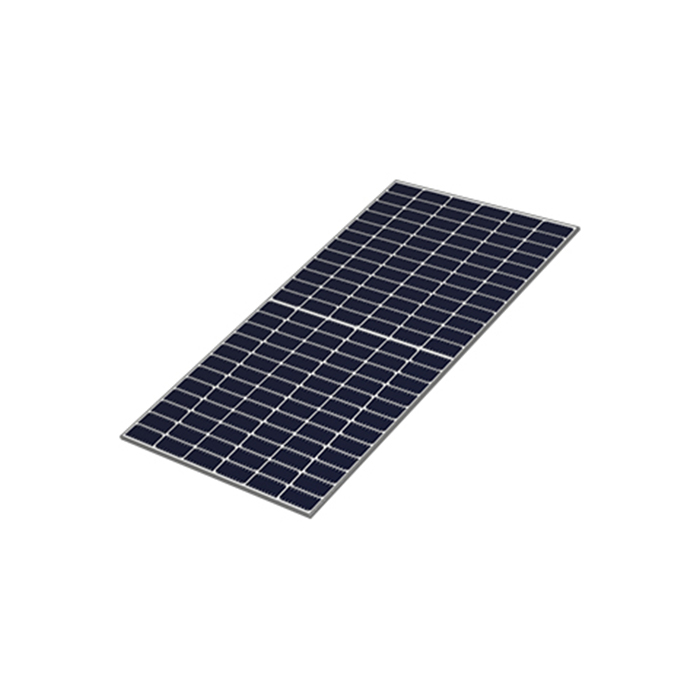
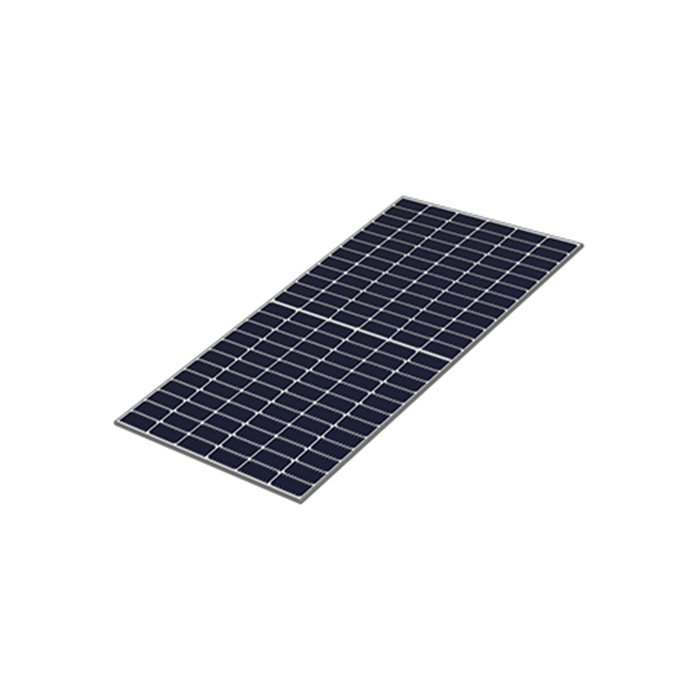
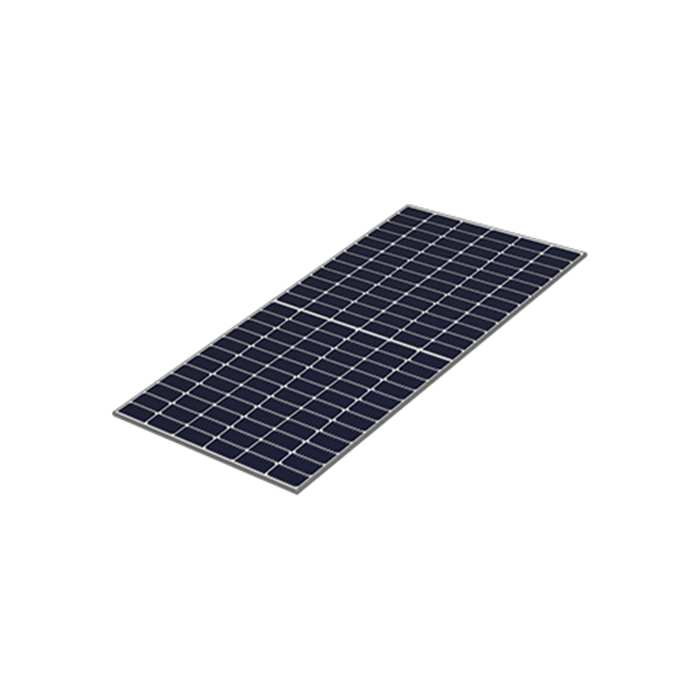
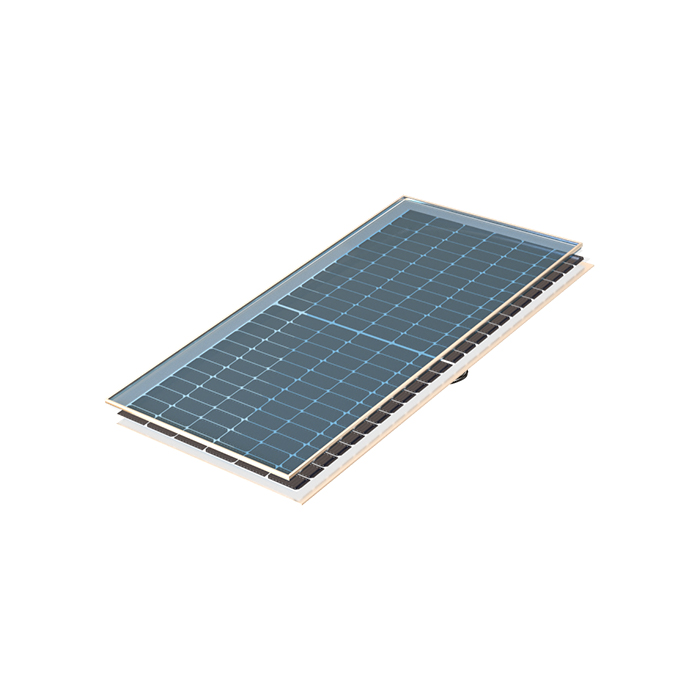
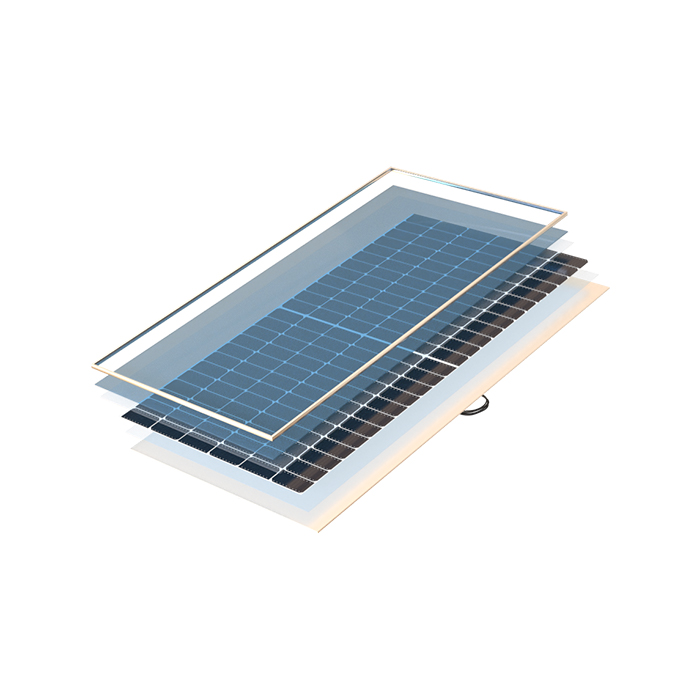
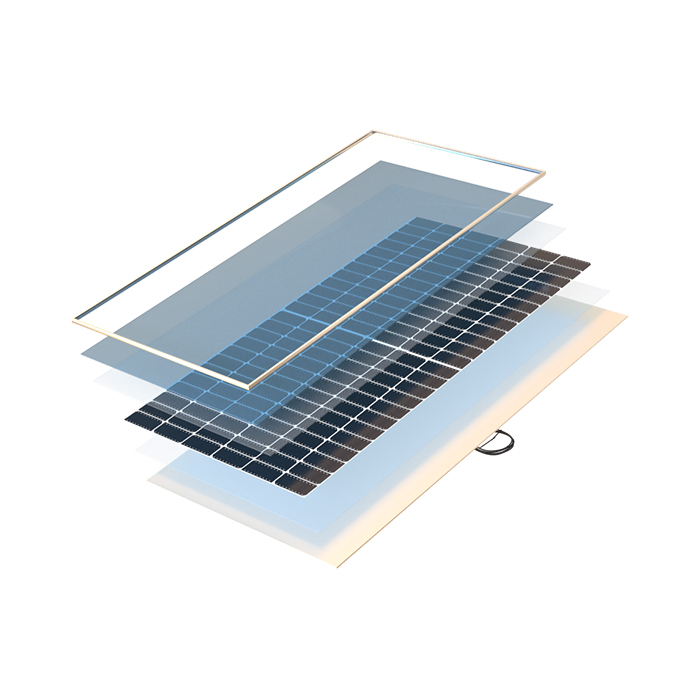
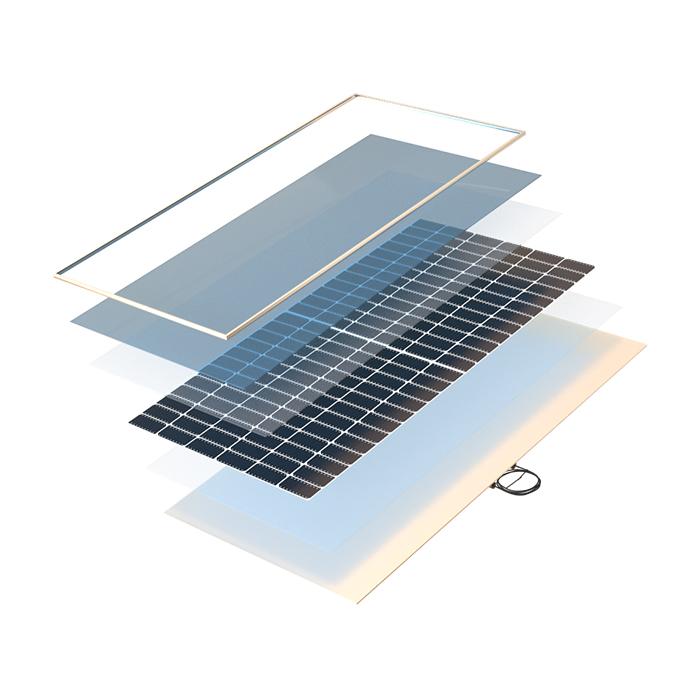
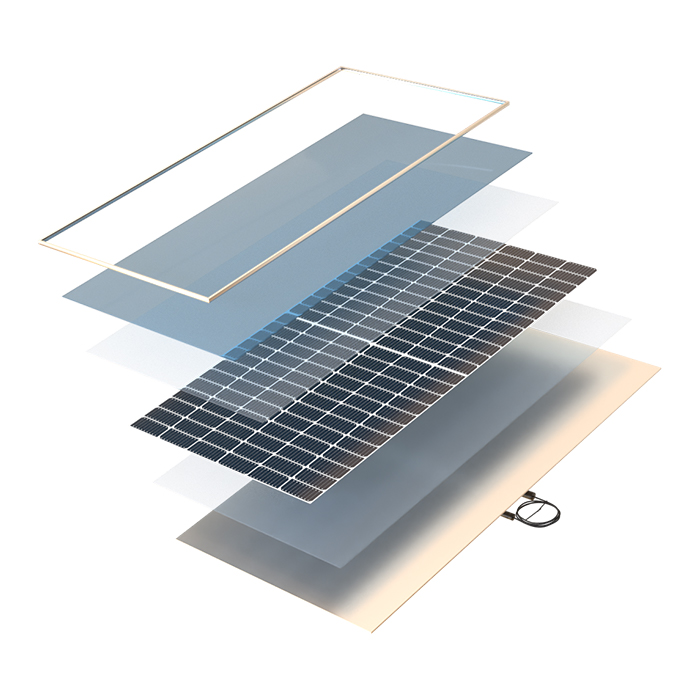
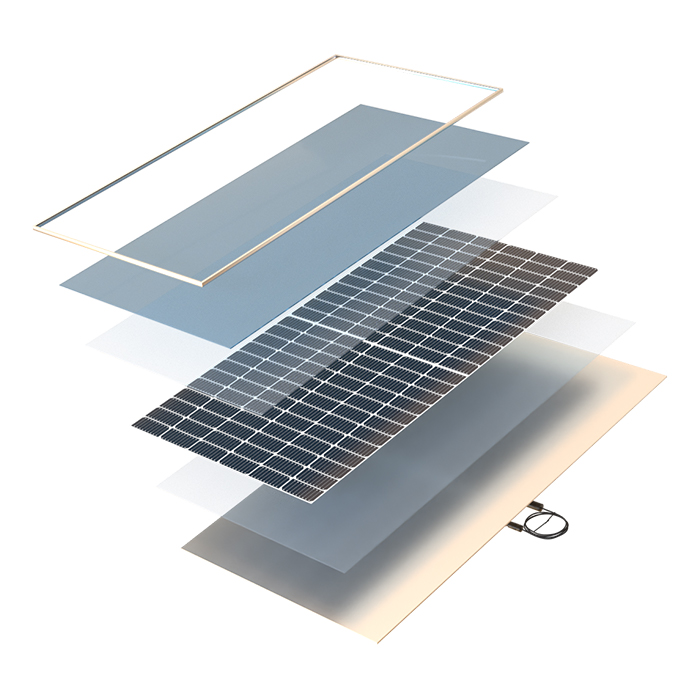
Frame & Adhesives
View DetailsGlass & Glass Coating
View DetailsSolar Cell Layer
View DetailsBacksheet or Rear Glass
View DetailsGo Inside a PV Module
Although Top Performers are listed in the Scorecard by model type, they represent unique bills of materials (BOMs) that PVEL has tested in our Product Qualification Program (PQP).
Scroll to explore the materials of a PV module. Click on labels to see how many types of each component were used in the BOMs tested for the 2023 Scorecard.
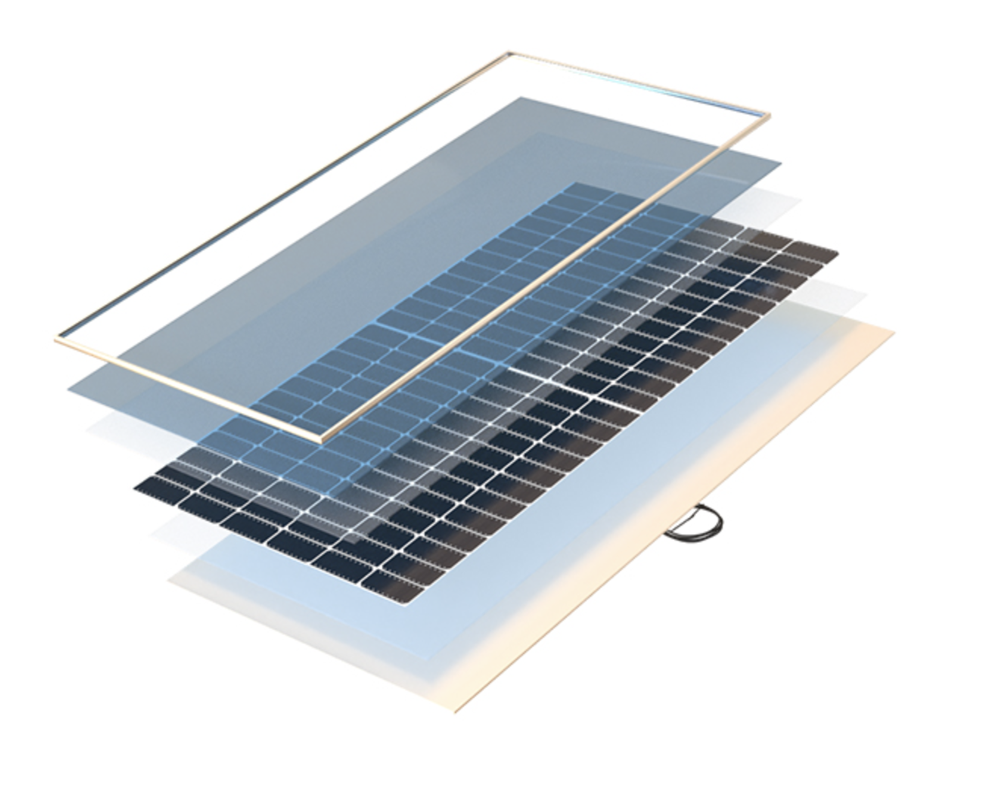
Frame
Frame heights tested for this Scorecard: 6
Frame Adhesive
Frame adhesive types tested for this Scorecard: 15
Front Glass
Suppliers tested for this Scorecard: 12
Glass Coating
Models tested for this Scorecard: 24
Front Encapsulant
Models tested for this Scorecard: 27
Cells
Manufacturers tested for this Scorecard: 23
Interconnects
Types tested for this Scorecard: >15Flux
BOM data
14 different flux models were tested for this Scorecard.
Back Encapsulant
Models tested for this Scorecard: 33
Backsheet or Glass
Types tested for this Scorecard: 34
71% of BOMs used a backsheet; 29% used rear glass
Junction Box
Suppliers tested for this Scorecard: 18
Junction Box Pottant
Pottant types tested for this Scorecard: 14
Diodes
Suppliers tested for this Scorecard: 23
Junction Box Adhesive
Adhesive types tested for this Scorecard: 15
Connectors
Suppliers tested for this Scorecard: 17
Why BOM-Level Testing is Important
PV modules with the exact same model type can be manufactured from completely different BOMs. PVEL’s test results from the lab and field demonstrate that individual PV module components can dramatically affect product quality. Suppliers are free to mix-and-match integral materials – even cells – as long as all the components are listed in the manufacturer’s IEC certification report. PVEL’s extended testing results have repeatedly shown that IEC certification testing is not sufficient to differentiate levels of long-term module reliability for project investors.
PVEL’s testing generates vital procurement intelligence.
While individual BOMs are not marketed to buyers, the detailed PQP reports clearly document the BOMs of each model that performed well in testing. PVEL’s downstream partners can leverage PQP reports to specify BOMs in supply agreements.
Over their 155 GW of aerial scans, Heliolytics has seen that the module model type is indicative but not sufficient for understanding module reliability risks. This example shows two adjacent modules that are the same model type but clearly different cells and likely other BOM components. The module on the right is performing as expected, but the one on the left has evidence of busbar discoloration. This can lead to module-level degradation, as well as differential degradation within the array, thus amplifying mismatch losses and further impacting site performance.
Testing PV Module Reliability and Performance
PVEL’s PV Module PQP is a comprehensive protocol of lab and field tests that assess the bankability of PV modules. Click here to view PQP test sequences. While the specific tests have changed over time, the same four principles have guided PVEL’s PQP since it was first established in 2012:
Empirical Data
The PQP provides empirical data for revenue and energy yield modeling.
Standard Processes
The PQP tests all BOMs consistently, using calibrated equipment overseen by PVEL’s experts via testing at PVEL’s facilities in California, USA, or at PVEL’s partner lab within the Kiwa Group, PI China, in Suzhou, China.
No Hand-picked Samples
PVEL’s inspectors witness the production of all test samples and record BOM details.
Regular Program Updates
PVEL implements biennial PQP test sequence updates targeting new technologies and manufacturing techniques.
How BOMs are Scored
To be eligible for the Scorecard, manufacturers must have:
- Completed the PQP sample production factory witness within 18 months of 2023.
- Submitted at least two factory-witnessed PV module samples to all PQP reliability tests, as per PVEL’s BOM test requirements.
The 2023 PV Module Reliability Scorecard shows Top Performers for six PQP test categories.
Top Performers are determined by averaging that specific test’s results for every BOM tested by PVEL that is sold under the same model type. Top Performers in each of the reliability tests appearing in the Scorecard must have < 2% power degradation following the particular test, a consistent Top Performer threshold since the 2018 Scorecard. For that reliability test they must not have experienced a wet leakage failure, a ‘major’ defect during visual inspection, or a diode failure. PAN Performance Top Performers must place in the top quartile for energy yield in PVEL’s PVsyst simulations.
Not all products or model types are represented in every test. Manufacturers can choose not to be listed in the Scorecard. In some cases, test results for some test categories were not available at the time of publication.